taylor bar impact test|taylor impact test plasticity model : manufacture 3D SPH simulation of classical Taylor-bar test. The investigation focuses on den- sity evolution approaches, material strength models, smoothing length adaptation Fapello.Downloader is just a downloader, i will not implement any AI to keep the project as simple as possible. If anyone then is interested in enhancing images and videos downloaded with FapelloDownloader, they can do so using one of .
{plog:ftitle_list}
WEBEpic Seven. aka Epic7 - A Korean mobile RPG developed by Super Creative, and published by Smilegate Megaport for Android and iOS. 157K Members. 454 Online.
During the Second World War, G.I. Taylor and colleagues developed an impact technique that enabled the compressive strengths of materials at strain rates of tens of .
The Taylor impact test (Taylor (86)) was originally devised as a means of determin- ing the dynamic yield strength of solids. The test involves the impact of a flat-nosed cylindrical projectile.3D SPH simulation of classical Taylor-bar test. The investigation focuses on den- sity evolution approaches, material strength models, smoothing length adaptationThe impact of a flat-ended cylindrical rod onto a rigid stationary anvil, often known as the Taylor impact test, is studied. An axisymmetric model is developed to capture the deformation behaviour of the rod after impact. The Taylor bar impact test, proposed by Taylor, 1948, Whiffin, 1948, Carrington and Gayler, 1948 as an experimental method to measure the dynamic yield strength of .
This report presents a critical discussion of the Taylor test, some of the experimental setups for its performance, and one current analysis of the test. In addition, actual experimental results are .
This paper presents an investigation of effects of various parameters used in 3D SPH simulation of classical Taylor-bar test. The investigation focuses on density evolution approaches, . Taylor impact test is the simplest experimental approach for characterizing plastic behaviour of metals under high strain rate (up to 10⁵ s−1). Herein, a cylindrical rod is impacted .
astm composite compression test
the taylor impact experiment
The Taylor bar is used in experiments to determine strain rate effects in metals. The input deck A is set up for a Lagrangian analysis. Elements at the bottom of the bar get highly deformed. Many researchers have investigated impact and explosion using SPH method, such as Taylor bar impacting on a solid wall [53], bird strike impacting on an aircraft wing [54], projectile impact and . The theoretical analysis by Taylor is well known as the Taylor model, and the corresponding Taylor test has become a standard procedure to determine dynamic yield stress of materials. In a Taylor test, strain-rate can reach as high as 10 4 s −1 , which is in the regime achievable between a Split–Hopkinson pressure bar and plate impact shear .The impact of a flat-ended cylindrical rod onto a rigid stationary anvil, often known as the Taylor impact test, is studied. . split-Hopkinson bar and torsion tests at ambient and elevated temperatures. But noting the unique strain and .
Classic Taylor-Bar Impact Test 1409 4. Benz’s particle adaptation scheme is easier to implement but with a similar accuracy, compared to Monaghan type in which smoothing factor has a significant influence on both accuracy and efficiency of the final solution. 5. The numerical results are sensitive to the artificial bulk viscosity parameter This information is useful because it helps to bridge the strain-rate gap between Split-Hopkinson pressure bar testing and the ultra-high rates achieved with plate impact experiments. 1997 Elsevier Science Ltd. INTRODUCTION The Taylor test [1, 2] is a useful high rate materials test in which strain-rates of 104-105 s- 1 can be easily realized .
Very recently, the Taylor impact test is instrumented to measure the stress–strain curve directly in such range of strain rate [36]. . Ultra high speed DIC and virtual fields method analysis of a three point bending impact test on an aluminium bar. Exp Mech, 51 (2011), pp. 537-563, 10.1007/s11340-010-9402-y. View in Scopus Google Scholar The Taylor test used the same 12.7 mm diameter, direct impact Hopkinson bar apparatus, however, instead of employing an impact bar to strike the sample, the specimen itself was projected from a commercial fastener gun to impact the end of the measuring bar.
Taylor impact test is the simplest experimental approach for characterizing plastic behaviour of metals under high strain rate (up to 10⁵ s−1).In materials science, the Charpy impact test, also known as the Charpy V-notch test, is a standardized high strain rate test which determines the amount of energy absorbed by a material during fracture.Absorbed energy is a measure of the material's notch toughness.It is widely used in industry, since it is easy to prepare and conduct and results can be obtained quickly and .
Taylor impact test is characterized by high impact energy, low cost, and good repeatability, giving it the technical foundation and development potential for application in high-g loading. The Taylor impact test typically consists of a cylindrical rod/bar/projectile striking a flat, rigid surface at high velocity to determine the dynamic properties of the rod/bar/projectile. During the test, the impact end of the rod/bar deforms plastically while . In the previous studies [2, 7], the accurate stress-strain curve was affected by the following two points.One is the extra oscillations [7] on the external force wave at the impact surface measured using the Hopkinson pressure bar. As pointed out by Gao and Iwamoto [7], initial steep spikes on the force wave were observed because of the Pochhammer [13] and .
Hopkinson Bar, Taylor impact tests or planar plate impact test investigations. At the Ernst-Mach-Institut (EMI), a variant of an inverted classical Taylor impact test is used by application of velocity interferometers of the VISAR type (“Modified Taylor Impact Test”, MTT). The conduction of the experiments is similar to that of planar . Although its use in dynamic applications has been more limited, 3D DIC has been applied to Koskly bar testing [11, 12], terminal ballistics [13,14,15], blast [16, 17], and even Taylor impact testing studies [9, 18]. The only drawback of applying high-speed stereo DIC to high-rate phenomena (e.g., Taylor test) is the limited temporal and spatial . The definition of the Taylor impact test is that a cylindrical specimen is accelerated to impact normally on a rigid target to produce deformation or destruction. Taylor impact tests were conducted by using a .strain rates the Split Hopkinson pressure bar (SHPB) or Taylor’s test is necessary (Fig. 1). At lower strain rates the Taylor test or a high rate servo-hydraulic machine may be used. In this article, the Taylor test is used to define the dynamic behavior of material. The nonlinear strain rate sensitivity of materials at high strain rate is an
In a Taylor test, strain-rate can reach as high as 10 4 s −1, which is in the regime achievable between a Split–Hopkinson pressure bar and plate impact shear experiments. Subsequently, several analyses for the Taylor test have been proposed in order to modify or to simplify the Taylor model. A coupled thermomechanical analysis of the Taylor impact test considering flat-ended cylindrical specimens of different materials fired at several striking velocities is presented.Keywords: Taylor impact test; stress-strain curve; Hopkinson pressure bar; miniaturized testing apparatus; finite element simulation 1. Introduction The Taylor impact test, established by Taylor [1], is a quite simple impact compressive test. In this test, a cylindrical slender specimen is shot to, and strikes the surface of a rigid body wall.
In our previous study, a modified Taylor impact test instrumented using a Hopkinson pressure bar and high-speed imaging was proposed to obtain the stress-strain curve at any moment. In this method, only a linear change in the internal force with respect to the axial position in the plasticity-dominant region of the specimens was assumed. Numerical and experimental studies on specimens with integrated pulse-shaper used for the instrumented Taylor impact test to measure stress-strain curves at high rates of strain . was successfully obtained in the time history of the impact force using a specimen with a truncated cone head in Taylor impact testing with a Hopkinson pressure bar . Keywords: Taylor impact test, damage, oblique impact, element erosion, thermomechanical deformations, composite penetrator . Taylor Impact Test and Penetration of Reinforced Concrete Targets by Cylindrical Composite Rods Wesley Ballew (ABSTRACT)
In the impact test, a miniaturized testing apparatus based on the split Hopkinson pressure bar (SHPB) technique is introduced to achieve a similar level of strain rate as 104 s−1, to the Taylor . Semantic Scholar extracted view of "Taylor Impact Test and Penetration of Reinforced Concrete Targets by Cylindrical Composite Rods" by W. Ballew. Skip to search form Skip to main content Skip to account menu. Semantic Scholar's Logo. Search 221,807,390 papers from all fields of science. Search .A Taylor cylinder makes a good test case for physical regime sensitivity because it is known to be a sensitive validation test for strength modeling at high rates [23][24][25][26][27] [28], but . In this study, the Taylor bar impact test was conducted to investigate the dynamic deformation behavior of metallic materials in the high strain-rate region, using a high-speed photography system .
astm composite compression test 3 point bend test
Mechanical behavior and texture evolution of Mg rare-earth alloy WE43 is investigated for strain-rates 10 −3 /s to upwards of 10 5 /s for the two material conditions - as-cast (AC) and T6 age hardened, rolled plate (RT6). The high strain-rate behavior is tested using both Taylor cylinder impact tests (TC) and split Hopkinson pressure bar tests (SHB) and bulk .
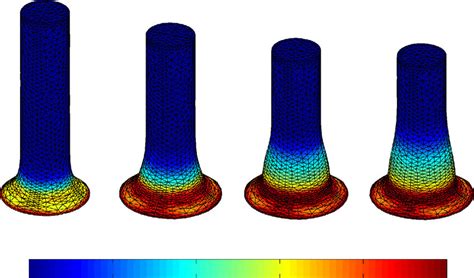
taylor impact test plasticity model
astm compression pile load test
taylor impact test
No nosso cronograma você consegue checar quais jogos estão passando hoje ou em qualquer dia da semana dentro ou fora do Brasil. Para acompanhar os jogos da Copa .
taylor bar impact test|taylor impact test plasticity model